When the pandemic struck earlier in the year, we decided we needed to move our prototypes from the workshop in Shenzhen (where we’d previously done all of our prototyping) to our office in California. However, turns out moving over a ton of machinery internationally is not as straightforward as one would hope.
The first thing to know is that freight shipping only bears a slight resemblance to package delivery services such as FedEx. When sending a package it’s a pretty simple process – put the item in a package, give it a destination, and then you’ll be charged accordingly. International freight works more like a marketplace, with options for whether you want goods to be delivered door-to-door, to a port, or some combination of the two. The main point of contact for the whole process is a freight forwarder, which is a company that books space on carrier ships or planes and arranges the documentation for shipments. There are hundreds (probably thousands) of freight forwarders to choose from, with no easy way to compare the various options. We used Freightos to find a reasonably priced freight forwarder, but their database is by no means exhaustive.
However, before even choosing a freight forwarder, we needed to get our prototypes packaged up. This was originally a bit of an afterthought for us, but getting crates designed and built to fit our prototypes and enable them to be transported in shipping containers ended up taking over two months and costing a quarter of the total shipping budget.
Mid-way through building a crate around Tensorbot Finished crate for robotic prototype
Once the crates were constructed, it was then time to load them in a shipping container. For ocean shipments, there is the option of either paying for an entire shipping container (known as a Full Container Load, or FCL), or just the volumetric space you are using (known as Less than a Container Load, or LCL). For any shipments greater than half a container in volume, FCL likely works out cheaper because the handling fees are lower.
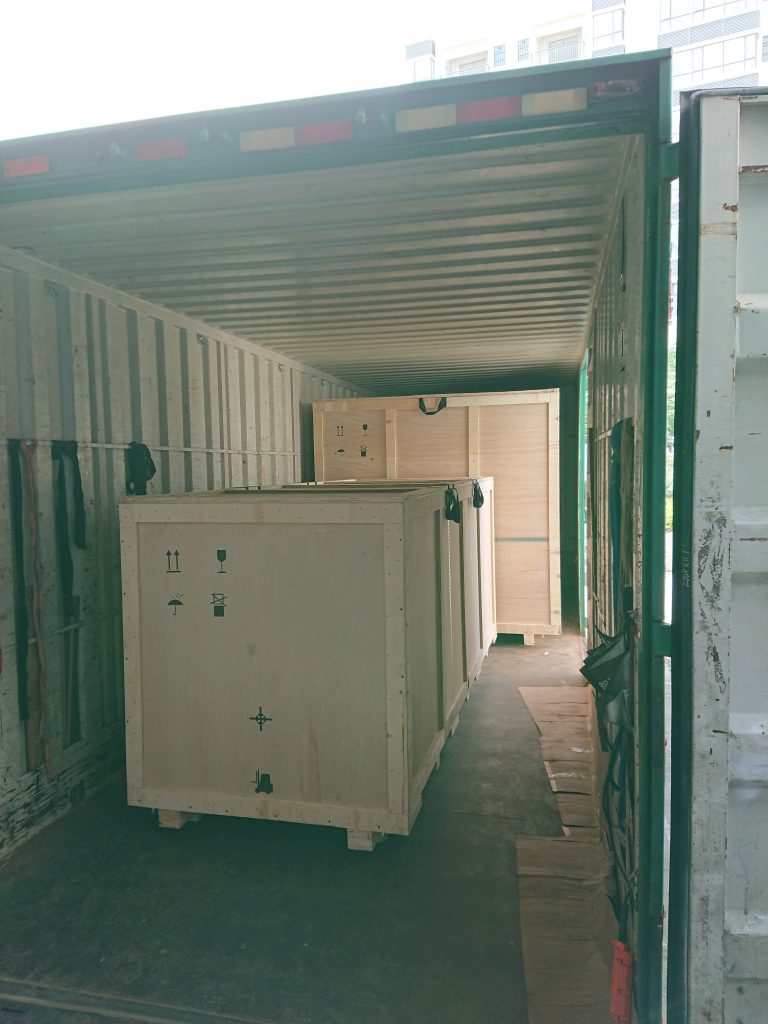
In total, including customs clearance, the shipment took 45 days to get from Shenzhen to Oakland (California). We used a customs broker to make the clearance process as seamless as possible. Though it’s not strictly necessary, having someone else deal with things like entry bonds for importing and HS codes makes it a lot easier.
After the crates were released from the port, we then contracted a local hauling company to deliver them to our office. When originally planning out the shipment, this was one of the parts I was most unsure about as the freight forwarding company wouldn’t deliver crates as big as ours to any business without a loading dock. However, it turned out to be light work with the right equipment.
After months in transit, our prototypes finally arrived safely!
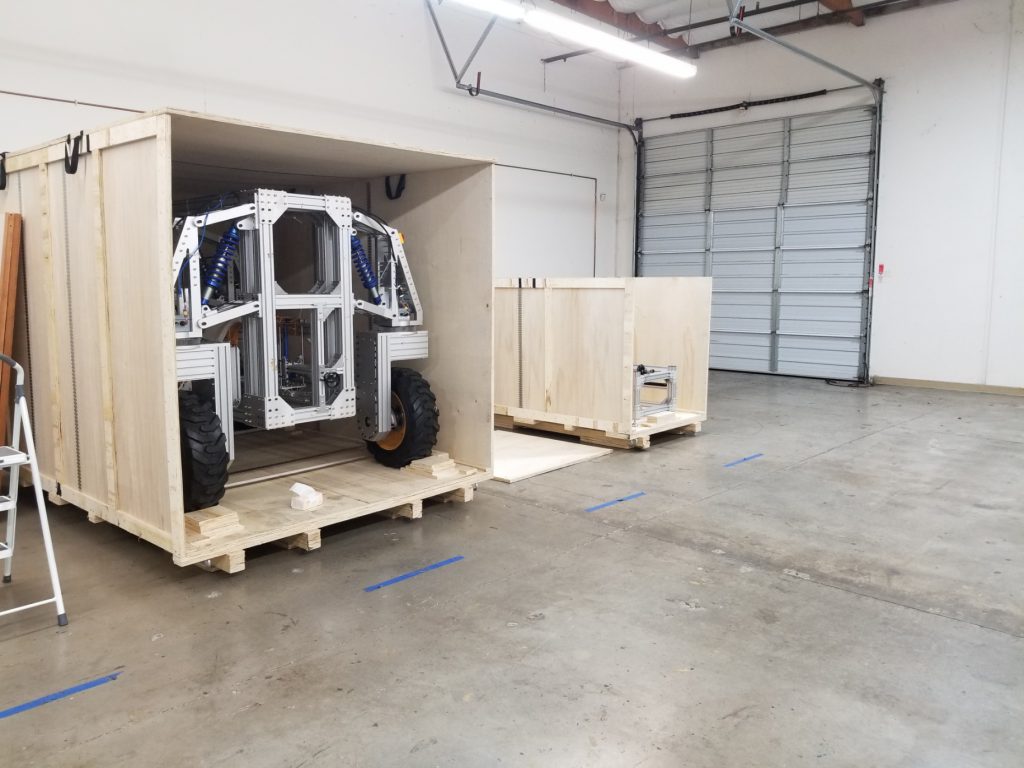